Fitting a new speedometer cable
The Video Course teaches you everything about modern cars.
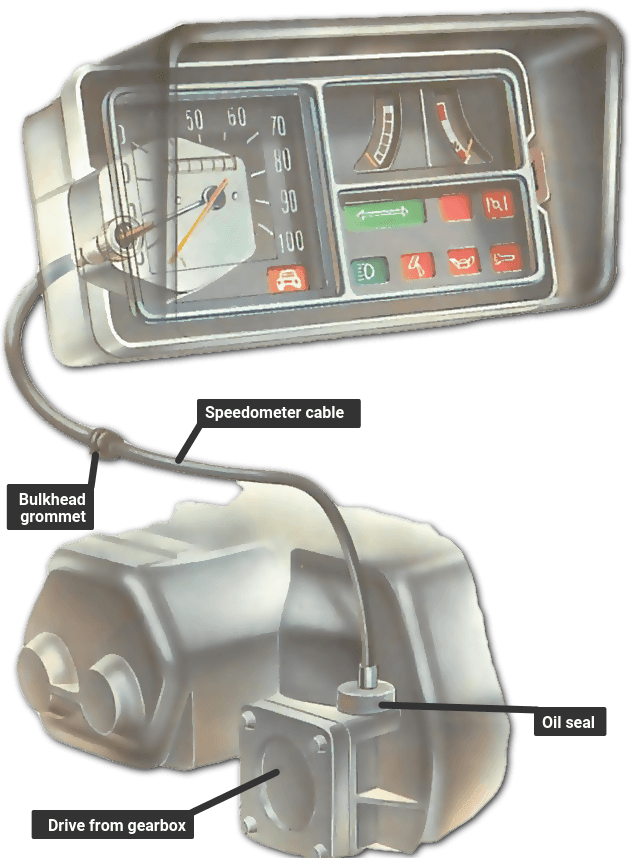
Speedometer failure is likely to be caused by a fault in the cable that runs from the gearbox to the back of the speedometer gauge.
If the gauge needle does not move at all, the inner cable or drive may be broken; or the cable's square ends may have become rounded with wear and fail to engage in the sockets.
The fixings at the ends can work loose or be wrongly fitted.
If the gauge needle swings or moves sluggishly, gearbox oil may have seeped up the cable and got into the speedometer itself. In that case, you must replace the speedometer.
If the needle twitches rapidly, see whether the cable is crushed, kinked or too sharply bent. Intermittent twitches can be caused by loose connections or by worn and slipping ends on the cable.
A tapping noise is a sign of a damaged drive or lack of lubrication.
To examine the cable for any of these faults, support the car securely on axle stands or ramps.
Disconnecting and checking the cable
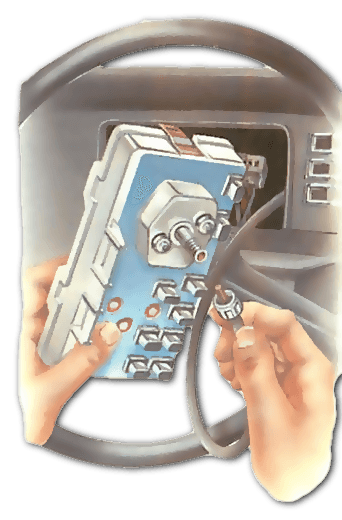
First look over the whole length of the outer cable to see if the casing is broken anywhere.
Make sure that the cable follows a smoothly curved route and is not kinked or crushed. There should be no bend within 50mm of either end. Bends elsewhere should have a radius of not less than 150mm.
On some cars, guide clips hold the cable in place. Make sure that it has not worked loose.
The cable is connected to the gearbox by a knurled thimble nut, a circlip, or a forked plate .
Unscrew a thimble nut with your fingers, starting it with large grips if necessary. Squeeze a circlip free with circlip pliers.
A single screw holds a forked retaining plate. Unscrew it.
The top end of the cable is harder to reach. If you cannot reach it, remove the speedometer or the instrument panel.
The top connection is a knurled thimble nut, or one of several types of clip. Most clips release when they are pushed in and turned sideways; one type has a ribbed area on one side, which you depress to release the clip.
Examine the square ends of the drive for wear and check that the fixings are sound.
Turn one end of the drive by hand while a helper watches the other end. If the other end does not turn, the drive is broken. If the drive turns stiffly or you feel it snagging, check that it is not kinked or crushed by a sharp bend or a guide clip.
If one end of the drive moves in a circle instead of revolving on the spot, the drive is kinked.
If the drive seems undamaged but is generally stiff, it may need lubrication.
Pull the drive out of the casing, clean the drive with petrol, smear it sparingly with grease and slide it back.
Some inner cables, however, have captive ends and you cannot pull them out. In that case, feed light oil between the cable and outer sheath.
Fitting the new cable assembly
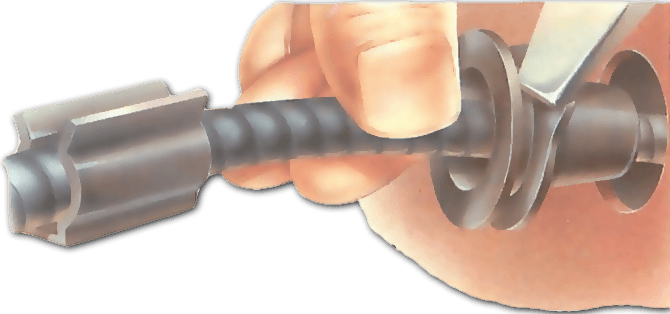
Find and release all the guide clips, and lever out the rubber grommet where the cable passes through the bulkhead. Pull the cable out into the engine compartment.
Check again that you need a new cable. Repeat the turning test to see if the drive is kinked; or pull out the drive and roll it along a flat surface. Hold the cable in a 'U' shape about 230mm wide. Turn one end of the drive. It should move smoothly without catching inside the casing.
Sometimes you can renew the drive alone, but makers now tend to supply only complete cables. In any case, take the old cable to the parts store to make sure that the new one is identical. It is a good idea to buy a new gearbox oil seal at the same time.
Push the top end of the new cable through the bulkhead. Use a thin screwdriver to ease the grommet into place.
Refit the cable into its guide clips. Some clips have bands to mark the points that should fit into the clip. They are a useful check that you are routing the cable correctly.
In any case, make sure that the route is smoothly curved. Add extra clips or bands only if they are really needed. Make sure that clips do not squeeze or pull the cable.
To fit the new gearbox oil seal , lever out the old one with a screwdriver and press in the new one, making sure it seats well.
Refit the lower drive connection, taking care that the square drive end is engaged. Tighten a thimble nut only finger tight, and be careful not to cross-thread it.
The top connection is slightly harder to refit, because it is more difficult to get the second end of the drive engaged.
Refit the speedometer if you had to remove it, and test it by taking the car on a short run.
Cable connections into the gearbox
Speedometer cable connections to the gearbox fall mainly into three types.
The knurled thimble-but connection is threaded inside, and screws on to the gearbox speedometer outlet - which is also threaded - up to the shoulder.
The circlip connection fits over the cable and into a recess in the gearbox output sleeve , securing both.
The fork connection - an older type - is simply a shaped fork that holds the cable end in the gearbox by means of spring pressure . It is secured by a screw.
The Ultimate Car Mechanics video course
Learn everything about modern cars from our new video series.
Learn more >-
We build a Mazda MX5 Miata from scratch
We start by tearing down and then rebuilding the whole car.
-
Every part explained
There's ridiculous detail on every part. Clearly and easily explained.
-
All modeled in 3D
We've created the most detailed 3D model ever produced so we can show you everything working.