How manual gearboxes work
The Video Course teaches you everything about modern cars.
Internal-combustion engines run at high speeds, so a reduction in gearing is necessary to transmit power to the drive wheels, which turn much more slowly.
The gearbox provides a selection of gears for different driving conditions: standing start, climbing a hill, or cruising on level surfaces. The lower the gear, the slower the road wheels turn in relation to the engine speed.
The constant-mesh gearbox
The gearbox is the second stage in the transmission system, after the clutch . It is usually bolted to the rear of the engine , with the clutch between them.
Modern cars with manual transmissions have four or five forward speeds and one reverse, as well as a neutral position.
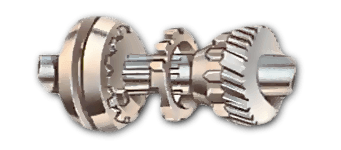
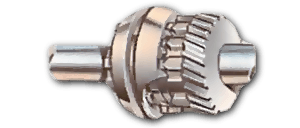
The gear lever , operated by the driver, is connected to a series of selector rods in the top or side of the gearbox. The selector rods lie parallel with shafts carrying the gears.
The most popular design is the constant-mesh gearbox. It has three shafts: the input shaft , the layshaft and the mainshaft, which run in bearings in the gearbox casing.
There is also a shaft on which the reverse-gear idler pinion rotates.
The engine drives the input shaft, which drives the layshaft. The layshaft rotates the gears on the mainshaft, but these rotate freely until they are locked by means of the synchromesh device, which is splined to the shaft.
It is the synchromesh device which is actually operated by the driver, through a selector rod with a fork on it which moves the synchromesh to engage the gear.
The baulk ring, a delaying device in the synchromesh, is the final refinement in the modern gearbox. It prevents engagement of a gear until the shaft speeds are synchronised.
On some cars an additional gear, called overdrive , is fitted. It is higher than top gear and so gives economic driving at cruising speeds.
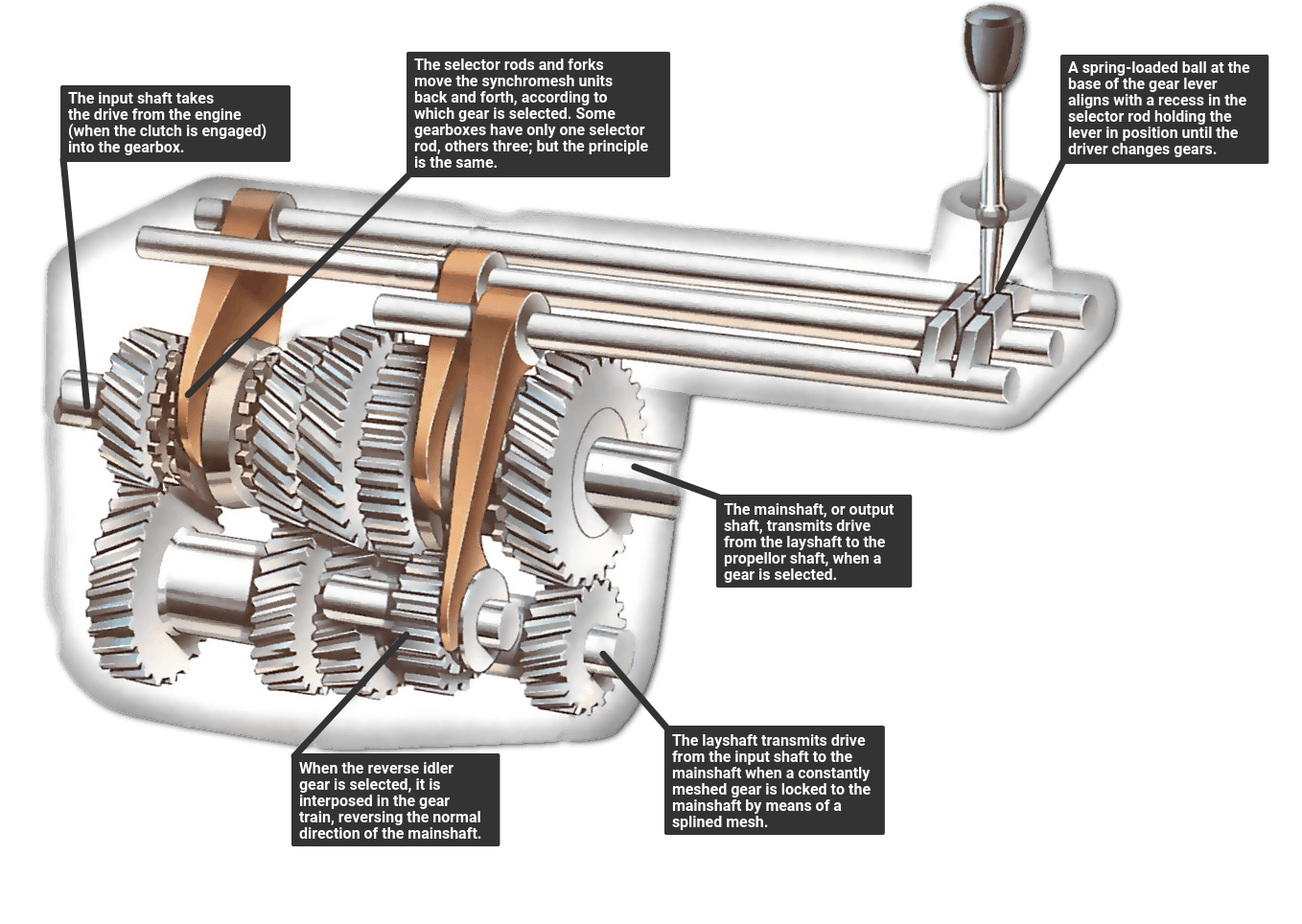
How gear ratios work
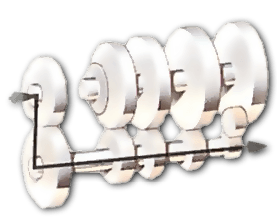
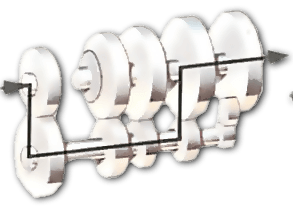
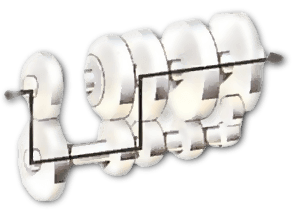

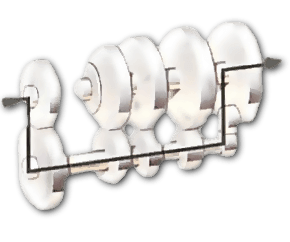
Synchronising the gears
The synchromesh device is a ring with teeth on the inside that is mounted on a toothed hub which is splined to the shaft.
When the driver selects a gear, matching cone-shaped friction surfaces on the hub and the gear transmit drive, from the turning gear through the hub to the shaft, synchronising the speeds of the two shafts.
With further movement of the gear lever, the ring moves along the hub for a short distance, until its teeth mesh with bevelled dog teeth on the side of the gear, so that splined hub and gear are locked together.
Modern designs also include a baulk ring, interposed between the friction surfaces. The baulk ring also has dog teeth; it is made of softer metal and is a looser fit on the shaft than the hub.
The baulk ring must be located precisely on the side of the hub, by means of lugs or 'fingers', before its teeth will line up with those on the ring.
In the time it takes to locate itself, the speeds of the shafts have been synchronised, so that the driver cannot make any teeth clash, and the synchromesh is said to be 'unbeatable'.
The Ultimate Car Mechanics video course
Learn everything about modern cars from our new video series.
Learn more >-
We build a Mazda MX5 Miata from scratch
We start by tearing down and then rebuilding the whole car.
-
Every part explained
There's ridiculous detail on every part. Clearly and easily explained.
-
All modeled in 3D
We've created the most detailed 3D model ever produced so we can show you everything working.