How car oil is refined
The Video Course teaches you everything about modern cars.
The fuel used in a modern car, whether petrol, diesel or even LPG ( Liquid Petroleum Gas ), has to meet high standards of purity if the car's engine is to run smoothly.
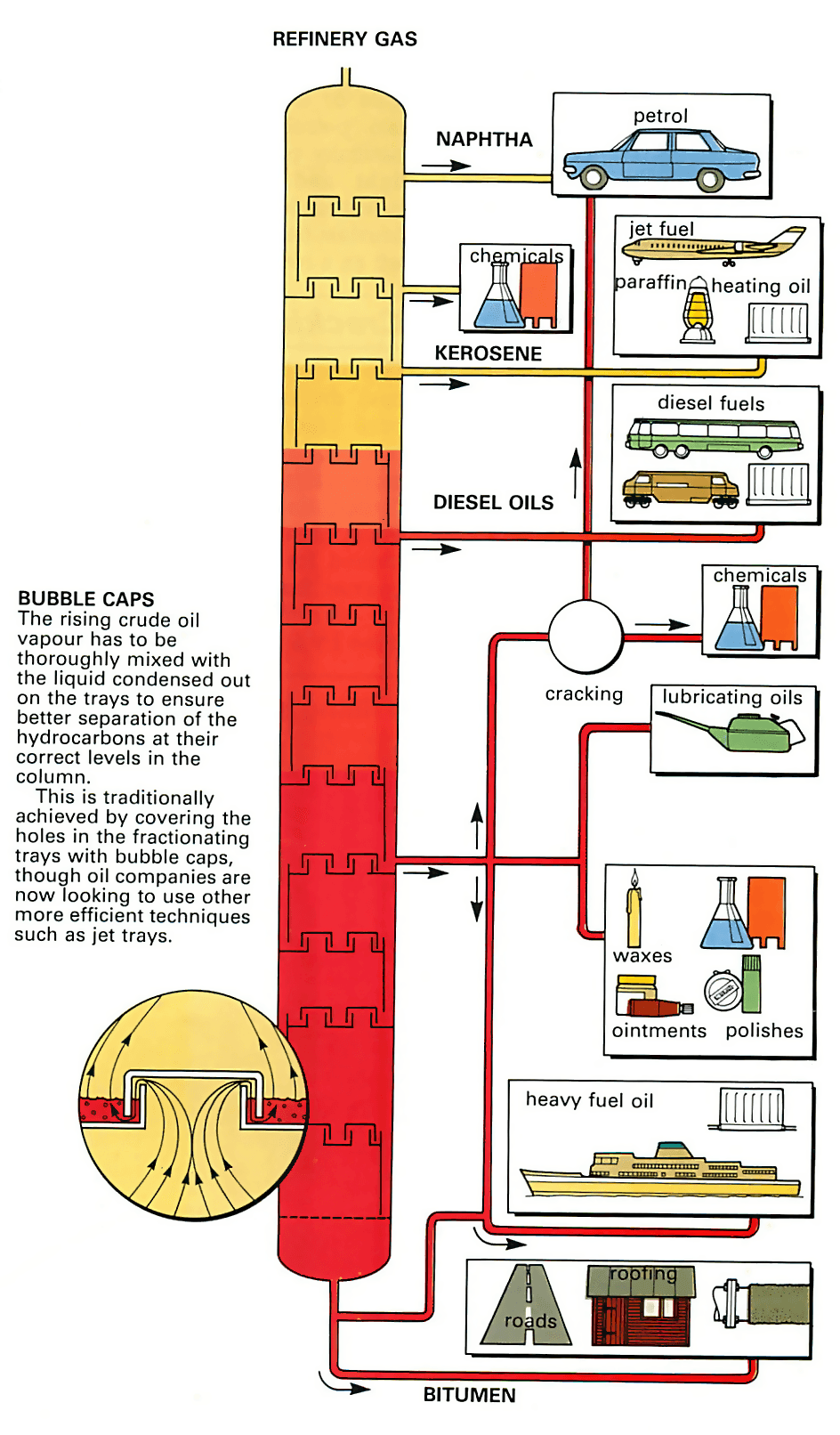
Modern fuels have to be sufficiently volatile to ignite quickly, even under adverse conditions, and they have to have the correct blend of hydrocarbons to burn evenly enough to develop useful power in an internal combustion engine . The fuel must also have the right octane value to prevent pinking (detonating too early) which can cause engine damage.
Internal combustion engines are tailored to run on a particular grade of fuel and tuned to run quite close to the limits which that fuel can support, so consistent quality is important in modern fuels.
Both petrol and diesel are derived from crude oil, which is a complex mixture of many hundreds of different hydrocarbons as well as other products which need to be removed during refining. Crude oils vary from source to source; they generally contain light volatile liquids, petrol among others, as well as much heavier, almost solid constituents, such as bitumen.
Separating out and purifying petrol and diesel from crude oil requires complex processes, which are carried out in an oil refinery.
Refining
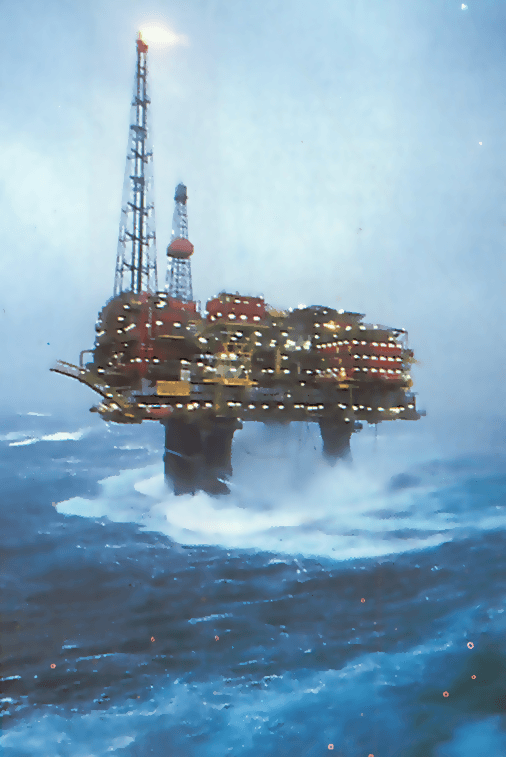
The oil is refined into its constituents by a process called fractional distillation . This separates out the different constituents of crude oil by making use of the fact that they boil off and vaporize at different temperatures.
The first process is carried out in a fractionating column, a tall cylindrical tower up to 250ft (75m) high, inside which are between 30 and 40 trays called fractionating trays, stacked one above the other. The bottom of the column is kept very hot but the temperature drops the further you move up the column, so that each tray is slightly cooler than the one below it.
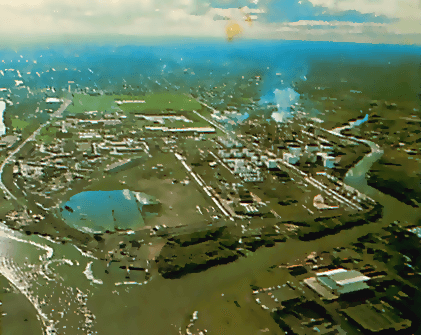
The crude oil is preheated to between 315°C and 370°C so that all except the heaviest constituents vaporize. It is then fed in towards the bottom of the fractionating column as a mixture of gas and liquid. The oil vapour rises up the column through devices, such as bubble caps, in the fractionating trays which cause it to be thoroughly mixed with the liquid already there. The heavier, still-liquid oil passes down to the bottom of the column.
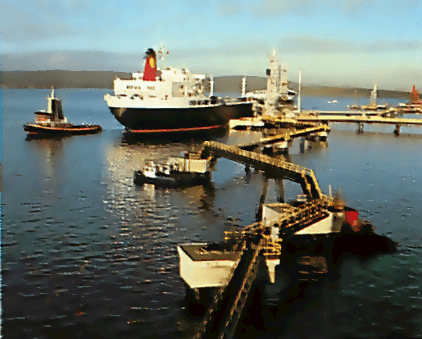
As the vapour rises it cools in line with the falling temperature of the trays. Whenever the vapour passes up to and bubbles through a tray containing liquid whose temperature corresponds to the boiling point of one of the constituents of the vapour, that constituent condenses out on the tray. The other, higher-boiling-point vapours carry on up the column.
The fractions
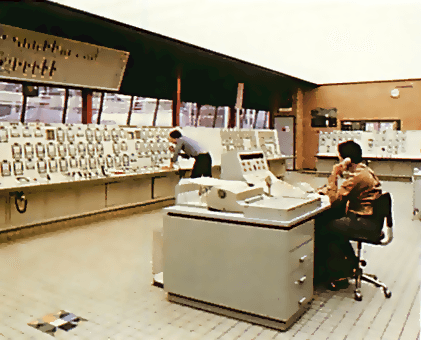
In this way, each constituent in the vapour meets a tray on which it condenses out. The result is a series of separated constituents, called fractions, which can be drawn off from the column through pipes.
There are six main fractions. The lightest, which is still a gas when it reaches the top of the column, is called refinery gas and is used as a fuel by the refinery itself.
The rest is further processed in an additional plant. The lightest of the resulting liquid fractions are very volatile and are used for blending into petrol.
Then come naphtha (used for further processing into petrochemicals or alternatively for blending into petrol), kerosene (which is basically paraffin), diesel oils and light and heavy oils used for industrial lubricating, and then the heaviest fraction, bitumen, which is left as a residue.
Cracking
The basic fractional distillation process divides up crude oil into its pure chemical hydrocarbons. But some of these hydrocarbons are more valuable than others. In particular, the demand for petrol is much greater than for bitumen, or indeed for diesel. So some of the heavier fractions are converted at the oil refinery into petrol. This is done by a process called cracking.
Thermal cracking uses heat in the process, while catalytic cracking uses a chemical catalyst.
In thermal cracking the hydrocarbons are heated to between 450°C and 540°C at high pressure . The result is a low-grade fuel which is then refined again at higher temperatures and pressures to produce petrol of good enough quality to use in car engines.
Catalytic cracking is more useful than thermal cracking since it gives a higher yield of useful products. By adding a catalyst (usually an aluminium-silica powder) to the oil during the pre-heating phase, the heavy fractions can be broken into a mixture of lighter ones, which are then fed into a fractionating column to be separated out.
These light fractions then undergo further processes called conversion processes to produce the correct mix of hydrocarbons.
Petrol properties

These conversions are followed by treatment stages where the appropriate additives are introduced to make the blended petrol suitable for winter or summer use.
To be useful for running internal combustion engines, petrol must have certain properties. It must burn smoothly in the engine over a wide range of speeds and power outputs without detonation . This manifests itself by 'knocking' and, if allowed to persist, can result in serious engine damage.
The petrol must have some readily volatile constituents which allow the engine to start easily in cold weather. But the petrol must not be so volatile that it vaporizes too easily and causes a lock in the fuel system, or even carburettor icing (see sideline, right).
The performance of petrol is gauged primarily by its octane number. To work this out, the petrol is compared with two standard fuels of known performance called n-heptane and iso-octane, both of which are hydrocarbons. N-heptane is a poor fuel for internal combustion engines and causes heavy knocking; it has an octane number of 0. Isooctane is the opposite, a very high quality fuel, and has an octane number of 100.
If petrol has an octane number of 90 this means that it gives a performance equivalent to a mixture of 90 parts iso-octane to 10 parts nheptane. Most car engines require petrol with an octane rating of between 90 and 100.
As a further anti-knock measure, it is still normal practice to add a small quantity of tetraethyl or tetra-methyl lead to the petrol. However, this is steadily being curtailed because of the poisonous nature of lead.
The maximum amount of lead allowed in petrol was lowered from 0.4 to 0.15 grammes per litre in 1986, and unleaded petrol is starting to appear on the European market. This is petrol to which no lead compounds have been added.
Diesel fuel
Diesel fuel is more viscous and heavier than petrol, is less volatile and comes off the fractionating column at a lower level.
Diesel fuel is not graded by octane rating like petrol; instead it is given a cetane rating. This is derived by comparing diesel with two other hydrocarbons, cetane and alpha-methylnaphthalene.
High-quality diesel fuel used in road-going vehicles has a cetane rating of about 50, while slower engines such as those used in large ships may run on fuel with a lower cetane rating. The higher the cetane rating, the easier the starting, the smoother the combustion and the lower the level of 'diesel knock '.
Some low-grade diesel (called gas oil) used for stationary or off-road work is dyed for identification and is thus known as red diesel. Only white diesel, which has had Road Tax Duty paid on it, can legally be used on the road.
Diesel fuel, like petrol, normally has important additives. Anti-freezing and anti-waxing agents have to be added to diesel fuel used in cold weather to stop it clogging in fuel lines and injectors .
Storage/transport
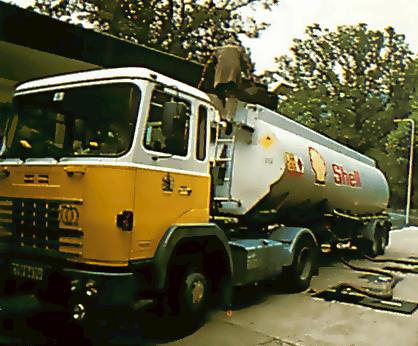
From the oil refinery, the petrol and diesel are transported to their garage and service station outlets by road or rail in specially designed tankers.
The fuels are usually stored in under ground tanks below the forecourt at the point of sale - the filling station. Petrol and diesel fuels are stored in separate tanks, as are different grades of petrol, until they are lifted to above ground level and metered for sale by the pumps .
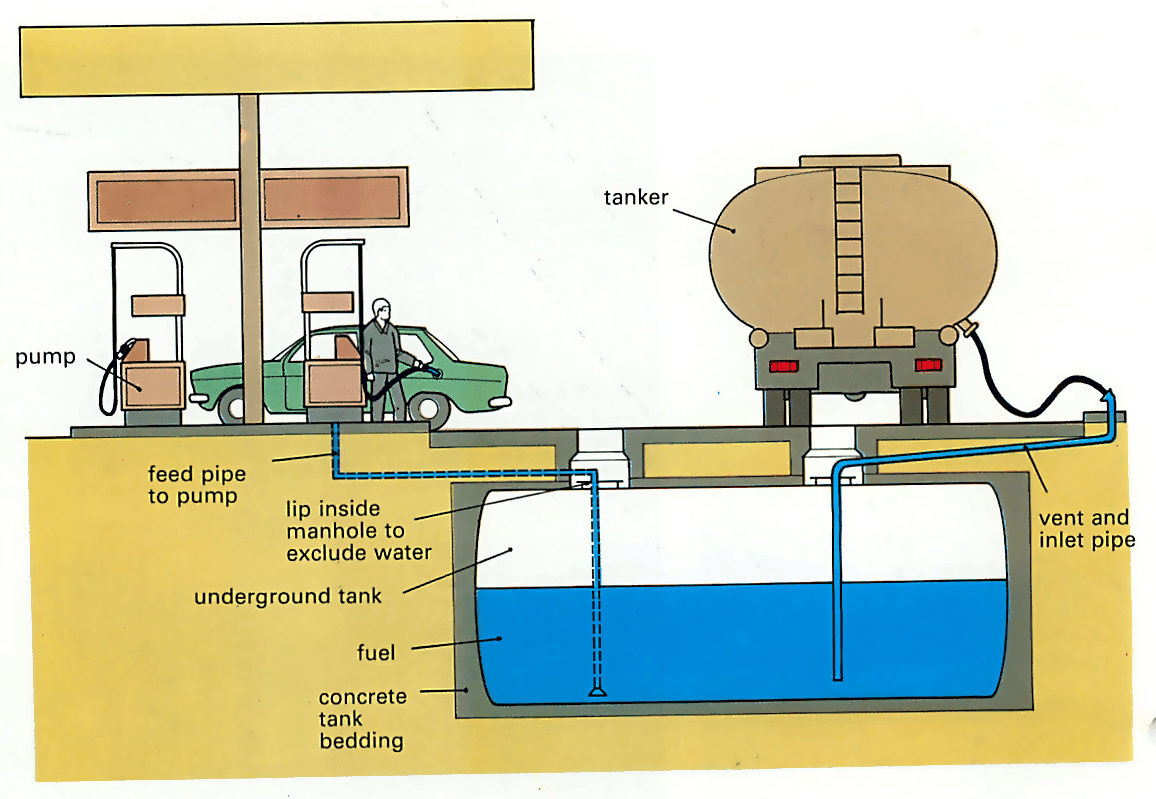
Petrol pumps can normally call up fuel from any of the underground tanks and blend it to supply the users with whichever grade is needed. However, leaded and unleaded petrol must not be mixed so they need separate tanks and pumps which must be clearly marked to show what they contain.
The Ultimate Car Mechanics video course
Learn everything about modern cars from our new video series.
Learn more >-
We build a Mazda MX5 Miata from scratch
We start by tearing down and then rebuilding the whole car.
-
Every part explained
There's ridiculous detail on every part. Clearly and easily explained.
-
All modeled in 3D
We've created the most detailed 3D model ever produced so we can show you everything working.